
China‘s dominance of the mining and refining of rare earth elements (REEs) poses a huge challenge to the West as it moves towards a carbon-neutral future.
There are 17 rare earth elements: yttrium and scandium and the 15 lanthanide elements (cerium, dysprosium, erbium, europium, gadolinium, holmium, lanthanum, lutetium, neodymium, praseodymium, promethium, samarium, terbium, thulium and ytterbium). These are divided into two categories according to their atomic numbers: light REEs and heavy REEs. Light ones include cerium, lanthanum, neodymium, praseodymium, samarium and scandium. Heavy ones include yttrium, terbium and dysprosium.
The metals – which have exceptional magnetic and conductive properties – are critical components of more than 200 products across a wide range of applications, including smartphones, computer hard drives, hybrid and electric vehicles (EVs), solar panels and flat screen monitors and televisions. Significant defence applications include electronic displays, guidance systems, lasers, and radar and sonar systems.
The role rare earths play in saving the Earth
Many experts say the metals are essential to the Western world’s ‘clean energy revolution‘ and the objective of carbon neutrality by 2050. They are also vital to the global technology revolution that is under way. For example, the bright colours of a smartphone display are produced by small amounts of yttrium, terbium and dysprosium. However, the single largest use of rare earths is in the manufacture of permanent magnets used in wind turbines, in the drive trains of EVs, and in energy-efficient applications. In fact, up to 600kg of REEs are required to operate just one wind turbine. About one kilogram is needed for every EV battery.
Among the light REEs, neodymium is seen as the most crucial, as it is the main element used in the creation of permanent magnets used in EVs. Praseodymium is often combined with neodymium to create even better magnets and blended with magnesium to form alloys that are important in aircraft engines. It is also used in studio lighting for the film industry. A small amount of the even scarcer heavy rare earths – dysprosium and terbium – is added to make permanent magnets for EVs that can operate at higher temperatures.
In 2020, 11.2 million EVs were operational globally, but the figure is projected to grow to 145 million by the end of this decade, according to the International Energy Agency. It could even jump to 230 million EVs by 2030 if governments accelerate their efforts to reach their carbon goals.
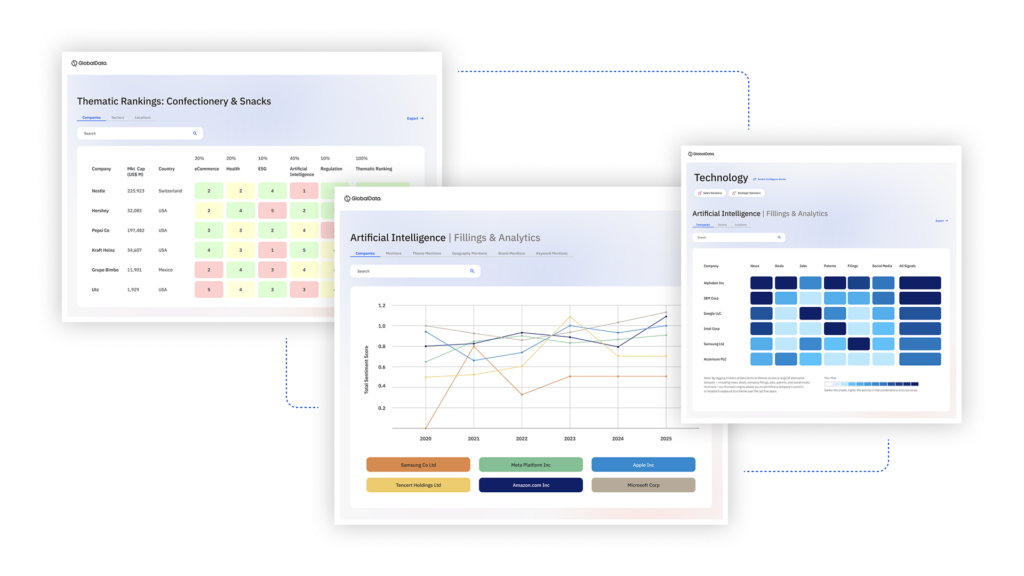
US Tariffs are shifting - will you react or anticipate?
Don’t let policy changes catch you off guard. Stay proactive with real-time data and expert analysis.
By GlobalDataTo achieve net zero by the middle of the century, the global cumulative installed capacity of onshore wind power must jump threefold by 2030 (to 1,787GW) and nine-fold by 2050 (to 5,044GW) from the installed capacity in 2018 (542GW), according to the International Renewable Energy Agency. If the world is to continue on the ‘clean revolution’ path, a great many permanent magnets will be necessary and in turn a huge amount of rare earths.
Can supply meet demand for rare earths?
The annual demand for REEs doubled to 125,000 metric tonnes (t) in the 15 years to 2021 and is projected to reach 315,000t in 2030. In May 2021, Adamas Intelligence forecast that the market for magnet rare earth oxides would surge fivefold from $2.98bn in 2021 to $15.65bn in 2030. Although rare earth oxides production worldwide is only worth several billions of dollars, it is essential for industries that are worth trillions.
This skyrocketing demand is causing prices to soar. The price of neodymium oxide has jumped from $47/kg in 2019 to $81/kg today, while that of praseodymium oxide has surged from $58.70/kg in 2019 to $89.10/kg today. Meanwhile, dysprosium oxide has surged from $206/kg in 2019 to $389/kg today and terbium oxide from $643/kg in 2019 to $1,016/kg, according to Tahuti Global, a Canada-based critical minerals consultancy. A coup d’état in Myanmar – the main foreign supplier of heavy rare earth feedstocks into China – in February this year has helped push the prices up.
For three decades, the Chinese government has had a strategic vision for the REE industry – something the West has lacked – and it now dominates the supply chain. In 2020, Chinese mines produced 140,000t of rare earths, almost 60% of total global mining output, according to the US Geological Survey (USGS). In 2020, the country also produced 85% of the world’s rare earth refined products, according to Roskill. About 70% of global production is consumed within the Chinese domestic market. Chinese production at both the mining and refined stages is controlled by quotas assigned to six state-owned enterprises, which are highly integrated throughout the rare earth supply chain.
The difficulty and danger in mining rare earths
There are, however, two main issues with the production of rare earths. First, all the rare earth deposits are mixed together, so it is hard and expensive for processors to separate them and to take advantage of their individual properties (and to split up the more valuable ones, such as terbium, from those of little value, like lanthanum).
We also need to consider new applications that will be developed from these elements, especially communications and more efficient technical applications of the future. Tim Harrison, Ionic Rare Earths
Second, REEs are bound up in mineral deposits with the low-level radioactive element, thorium, exposure to which has been linked to an increased risk of developing lung and pancreatic cancer. These obstacles create a huge challenge for any Western company that wants to become involved in the rare earths industry.
“REEs are extremely important to the global technology revolution that is under way,” says Tim Harrison, managing director of Ionic Rare Earths, an Australian company developing the Makuutu rare earths project in Uganda. “They will be required to facilitate the move towards carbon neutrality and to support the development of EVs and offshore wind turbine capacity that world governments want to implement to achieve the carbon targets. We also need to consider new applications that will be developed from these elements, especially communications and more efficient technical applications of the future.
“Right now it is hard to go past the magnet REEs – neodymium, praseodymium, dysprosium and terbium. These will be required to help facilitate the transition to carbon neutrality. Additionally, there are other REEs, such as erbium, which will be required to facilitate 5G communications networks and nuclear power, a range of heavy REEs that have very high-end applications, and yttrium in defence. As the world also looks to develop space transportation, some of the other REEs, such as scandium, will become more important.”
China has planet's biggest reserves of rare earths
There are more than 800 rare earth deposits known on the planet. They are not termed as rare because they are difficult to find, but are rare in chemistry terms because they behave the same chemically and so end up in mixed lots and are a little more difficult than other metals to separate from one another. They are relatively easy to extract; in fact, there are types of deposits in which a solution of fertiliser can be poured on the ore and the rare earths are then extracted. They are also stable and commonly shipped as oxides, or metal rust, so they are relatively easy to deal with. However, despite this abundance, it is unusual to find deposits of rare earths that are large enough and concentrated enough for commercial ore extraction. This contributes to rare earth mining taking place in just a few locations around the world.
According to the USGS report 2021, the total global reserves of REE amount to 120 million tonnes. Of this, China has the biggest reserves at 44 million tonnes, followed by Vietnam (22 million tonnes), Brazil (21 million tonnes), Russia (12 million tonnes), India (6.9 million tonnes), Australia (4.1 million tonnes), Greenland (1.5 million tonnes) and the US (1.5 million tonnes).
The total production of all REEs amounted to 240,000t in 2020, up from 220,000t in 2019, according to USGS. China's production quota was 140,000t in 2020, up from 132,000t in 2019. The US was the second-biggest producer in 2020 at 38,000t, followed by Myanmar (30,000t), Australia (17,000t) and Madagascar (8,000t).
Production from China is forecast to remain relatively flat until the end of the decade, according to Roskill. The flattening in Chinese domestic production from 2022 onwards will see demand for feedstock from some top Chinese-based rare earths processors increasingly being met by imported mineral concentrates.
Demand for permanent magnets to jump
According to Adamas Intelligence, total magnet rare earth oxide demand is forecast to jump at a compound annual growth rate (CAGR) of 9.7% between 2021 and 2030, while REE prices are projected to surge at a CAGR of between 5.6% and 9.9% over the same period.
From a technical point of view, the sexy REEs are the magnet materials. Jon Hykawy, Stormcrow Capital
It forecasts that global shortages of neodymium, praseodymium and didymium oxide (or oxide equivalent) will collectively rise to 16,000t in 2030, an amount equal to roughly three times the annual output of neodymium and praseodymium oxide of Lynas Corporation, an Australian producer. It also sees the undersupply of this oxide generating global shortages of neodymium-iron-boron alloy and powder (used in EV motors), amounting to 48,000t annually by 2030, roughly the amount needed for some 25–30 million EV traction motors.
EV traction motors, electric bicycles, commercial EV motors, electric scooters and motorcycles are expected to command a 23% share of all the demand for neodymium oxide powders and alloys across the world every year until the end of the decade. Adamas forecasts that the EV sector alone will consume one in every four tonnes of neodymium oxide powder or alloy produced worldwide in 2030.
In February 2021, the US rejoined the Paris Agreement on climate change and unveiled ambitious plans for electrifying the country's vehicle production and fleets. The US could join Europe and China as a major driver of the EV market’s growth during the rest of the decade.
"From a technical point of view, the sexy REEs are the magnet materials," says Jon Hykawy, president and director at Stormcrow Capital, a Canada-based critical materials research house. "The two common types of REE magnets are usually referred to as samarium-cobalt [SmCo] and neodymium-iron-boron [NdFeB], although these magnets commonly use two rare earths, neodymium and praseodymium. SmCo is a specialty material because of the scarcity and cost of both samarium and cobalt, but NdFeB is more common.
"Unfortunately, there is a problem with NdFeB. If the magnet heats up too much, as when you have put NdFeB magnets into a confined space, like the motor in an EV, and then strain that motor, say pulling a load up a tall hill, there is a significant danger that the magnets will heat up enough to reach a critical temperature and demagnetise, permanently. Your motor is now a paperweight, and that is not good. To effectively raise that temperature, manufacturers add some other REEs that are even scarcer and more expensive than neodymium and praseodymium, known as dysprosium and terbium."
He adds that the current bottleneck is neodymium and praseodymium to make magnets for everything from EVs to toy drones to appliances. However, as EV use continues to grow, the bottleneck is likely to become terbium and dysprosium.
Dysprosium and terbium supply bottlenecks
Today's thinking about how to optimise cash flow out of a rare earth mine is about maximising production of neodymium and praseodymium to to make greater amounts of small magnets, which are used to carry out tasks such as moving a car seat back and forth or adjusting side mirrors. However, if the auto industry wants large, high-end magnets that work at elevated temperatures, it will require many more tonnes of dysprosium and terbium, and these more rare elements will become the bottleneck.
"Demand growth of the 2020s will soon be dwarfed by the astronomical demand growth of the 2030s and therein lies the real defining challenge and opportunity facing the global rare earth industry today," said Adamas Intelligence in a report published in September 2020.
"Looking ahead to 2030, it is exceptionally challenging to foresee how – under any realistic scenario – the supply side of the rare earth industry will be able to keep up with rapidly growing demand for magnet rare earths (in other words, neodymium, praseodymium, dysprosium and terbium). Moreover, in attempting to keep up with magnet rare earth demand growth, it is equally challenging to foresee how the industry will be able to cope with mounting surpluses of other sacrificially overproduced rare earths, such as cerium and lanthanum."
It adds: "If the global industry continues to operate myopically – preparing, anticipating and investing only for a three to five-year outlook – the rate of demand growth for magnet rare earths will soon reach ‘escape velocity’."
The report also says that the point at which annual demand growth becomes so great – in other words, more than 6,000t per annum – is simply implausible for the already-lagging supply side to catch up and keep up. In order to avoid this outcome and to seize the enormous opportunity, a flood of Western investment is needed to develop new sources of supply and downstream value chains to convert that supply into metals, alloys, magnets and other materials used by high-tech industries globally.
Largest rare earth mines found in China
The biggest rare earth mines are located in China, but large mines are located all around the world. The Bayan Obo deposit in Inner Mongolia, north China – containing 40 million tonnes of rare earths reserves – houses the world’s largest deposits. The mine has been in production since 1957 and currently accounts for more than 70% of China’s light REE production.
China has pursued a 'scorched earth' policy in ramping up its rare earth production. It has caused an environmental disaster during the past 15 years and is not something the Western world would want to do. Simon Gardner-Bond, TechMet
Mount Weld Central Lanthanide Deposit (CLD), which is located inside an ancient collapsed volcano in Western Australia, is one of the highest-grade rare earth deposits in the world and is the largest rare earths mine outside China. During the second quarter of 2021, it produced 1,393t of neodymium-praseodymium, up from 775t during the same quarter of 2020. The deposit is owned by Lynas Corporation, which processes the CLD ore at the Mount Weld Concentration Plant. This produces a rare earth concentrate that is sent for further processing at Lynas Malaysia’s advanced material plant near Kuantan in Malaysia.
The Mountain Pass Mine, owned by MP Materials, a Las Vegas-based mining company, is an open-pit mine of rare earths on the south flank of the Clark Mountain Range, 85km south-west of Las Vegas. In 2020, the mine supplied 15.8% of the world's rare earth production and is the only rare earth mining and processing facility in the US.
"China dominates every stage of rare earths production and refining," says Simon Gardner-Bond, chief technical officer at TechMet, a UK-based investor in the technology metal supply chain. "Perhaps the West sleepwalked into China dominating the industry. In free market economies, it is very hard to force people to do something or to produce something. That requires government subsidies or grants to push a private sector company in a certain direction.
"It is not too difficult to find a rare earth deposit; the hard part is separating the rare earths inside the ore. Radioactivity can be an issue. China has pursued a 'scorched earth' policy in ramping up its rare earth production. It has caused an environmental disaster during the past 15 years and is not something the Western world would want to do."
Rare earth processing and radioactive waste
Production of rare earths metals generates large volumes of toxic and radioactive material, owing to the co-extraction of thorium and uranium – radioactive metals that can cause problems for the environment and human health.
In an article for the BBC in 2015, entitled 'The dystopian lake filled by the world’s tech lust', journalist Tim Maughan highlighted the pollution taking place in China. He wrote that, arguably, what makes neodymium and cerium – another REE widely used in the optics industry for the fine polishing of glass – scarce enough to be profitable are "the hugely hazardous and toxic process needed to extract them from the ore and to refine them into usable products".
He added: "For example, cerium is extracted by crushing mineral mixtures and dissolving them in sulphuric and nitric acid, and this has to be done on a huge industrial scale, resulting in a vast amount of poisonous waste as a by-product. It could be argued that China’s dominance of the rare earth market is less about geology and far more about the country’s willingness to take an environmental hit that other nations shy away from."
The Bayan Obo mine has generated a vast toxic lake close to Baotou, a city of 2.6 million people in northern China. Created by damming a river and flooding what was once farmland, the lake is a 'tailings pond', a dumping ground for waste by-products.
In June 2021, Baotou officially implemented a raft of new measures aimed at promoting the 'high-quality' development of the local rare earths industry. It will provide tailor-made subsidies and specific preferential policies for major projects of at least $9.13m (1bn yen) in domestic or foreign investment. Millions of yen are also being earmarked for rare earth research centres and laboratories.
Furthermore, toxic waste at the Lynas Advanced Materials Plant in Malaysia, operated by the Australian REE producer Lynas Corporation, has raised red flags. At the facility, concentrated ores are roasted with sulphuric acid to dissolve the rare earths and then diluted with water in a process called water leach purification, leaving a moist, paste-like residue. By September 2018, the Lynas plant had already produced 1.5 million tonnes of residue. The ore contains thorium and uranium and almost 30% of it is slightly radioactive.
Although Lynas ultimately received permission from the Malaysian government to operate the plant, it now has until 2023 to relocate the facility. It has identified a site at Kalgoorlie-Boulder, an outback town in Western Australia, where an environmental assessment and approval process is now under way.
Some rare earth oxide facilities elsewhere have built permanent, secure facilities to store such waste, according to Julie Klinger, a geographer and expert in rare earths mining at Boston University; others are secretive about what they do with it. If the West is to become a major part of the supply chain of REEs, it must find effective ways of carefully and economically managing the waste.
Rare earth projects around the world
In January 2021, the US government and Lynas Corporation agreed to build a commercial light rare earths separation plant in the US, with the US Department of Defense expected to provide $30m in funding and Lynas contributing another $30m. Once operational, the plant will produce about 5,000t of rare earth products annually, including 1,250t of neodymium-praseodymium, and will use feedstock material from a cracking and leaching operation the company is developing at Kalgoorlie-Boulder.
Lynas Corporation has also inked a deal with privately held Blue Line Corporation for rare earth processing operations in Texas. NioCorp Developments is developing a mine in Nebraska that aims to produce a rare earth element as a by-product. Texas Mineral Resources Corporation and privately held USA Rare Earth are working on projects in Texas and Colorado. Furthermore, Ucore Rare Metals has been developing a mine in Alaska and working on processing equipment.
According to mining experts, Bear Lodge, a small mountain range tucked away in the north-east corner of Wyoming state, about 65km from South Dakota’s border, is home to one of the richest and highest-grade rare earth deposits in the US, with an estimated 18 million tonnes of rare earths inside. Rare Earth Resources of Colorado is developing the site.
It is concerning that one country is so critical to the rare earths supply chain. Luisa Moreno, Tahuti Global
Other countries are determined to become part of the REE supply chain. In August 2020, the Russian government said it planned to invest $1.5bn (Rbs110bn) across 11 rare earths projects by 2030. It is offering reduced mining taxes and cheaper loans to investors in the projects. The incentives are designed to increase Russia’s share of global rare earths production to 10% by 2030, up from 1.3% in 2021, with production expected to reach 7,000t of rare earth concentrates by 2024.
In January 2020, Japanese state-owned agency Japan Oil, Gas and Metals National Corporation (Jogmec) signed an agreement with Namibia Critical Metals to jointly explore, develop and refine mineral products from the company’s Lofdal heavy rare earths project in north-western Namibia. For an investment of $20m in exploration and development, Jogmec will earn a 50% interest in the project.
Mkango Resources, a Canada-based rare earths developer, is exploring the Songwe Hills deposit – which features carbonatite-hosted rare earths – in south-eastern Malawi. Currently, it is carrying out a pre-feasibility study and expects to enter production in 2024. Together with Grupa Azoty Pulawy, a Polish chemicals producer, it wants to develop a rare earths separation plant in the Polish Special Economic Zone at Pulawy in eastern Poland.
Annual production from non-Chinese sources is forecast to jump from about 20,000t of REEs in 2020 to about 70,000t by 2030, according to Roskill. It says a very limited connecting supply chain exists to maintain the demand from production, so a lot of this material will likely end up being processed in China.
"It is concerning that one country is so critical to the supply chain," says Luisa Moreno, managing director at advisory firm Tahuti Global. "Refining – in particular of the heavy rare earths – is a big worry, as very little of it takes place outside of China. It is expensive to recycle rare earths, especially the heavy ones, and that is not the solution."
It is essential that Western countries come together – and provide subsidies if needed – so that the rare earths supply chain can be diversified. Chinese suppliers are likely to take care of their own customers closer to home first if any supply problems arise, as they are their best customers. Rare earths are essential to the clean and global technology revolutions that are taking place globally and the West must invest in environmentally friendly ways of processing these vital elements.