
Global Shipping Container Shortage on COVID-19
A year-and-a-half after Covid-19 first shook the world economy, logistics chaos continues to plague global supply chains.
The cost of transporting goods by container ship has doubled since May 2021, according to data from Freightos, taking the total increase over the past 12 months to 526%.
The high rates mask significant variation between routes, carriers and even customers. According to data analytics firm Xeneta, the cost of transporting goods across the Pacific last month ranged from $5,500 to $20,000.
Smaller companies are bearing the brunt of the price increases. As the Financial Times reported in August, carriers have been prioritising their relationships with larger, more reliable customers.
One reason may be a desire to lock the current freight rates into long-term contracts, contracts to which only the largest customers will be able to commit.
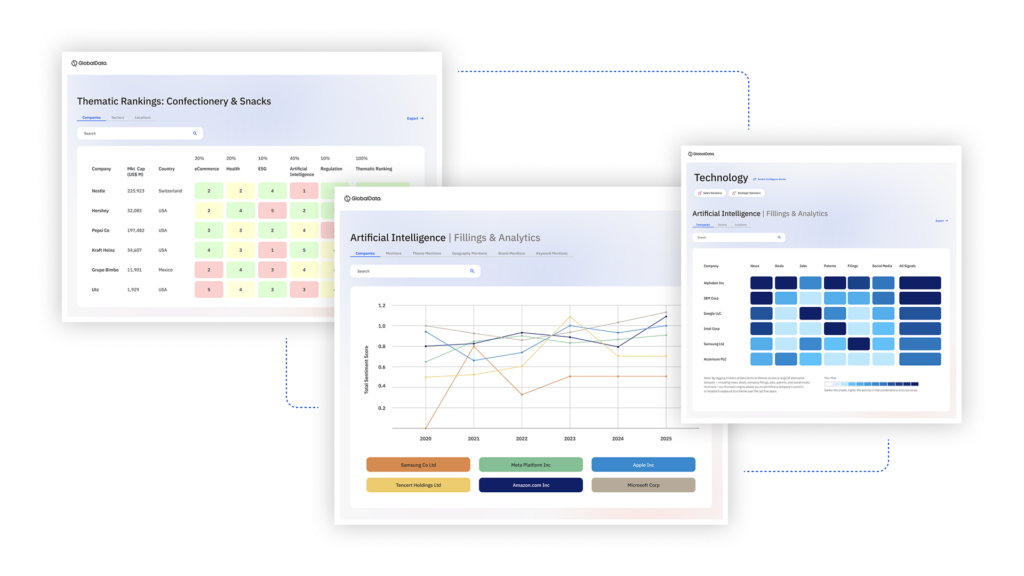
US Tariffs are shifting - will you react or anticipate?
Don’t let policy changes catch you off guard. Stay proactive with real-time data and expert analysis.
By GlobalDataWhere once these customers could expect 5% lower prices than their smaller competitors, today the difference is reportedly closer to 20%.
A logistical nightmare
As lockdowns shuttered offices and factories in March and April 2020, combined exports from the EU and US fell by 25%. Imports also fell, though only by 17%.
In China, by contrast, exports substantially outperformed imports. Imports fell by 5.8% between March and May 2020, whereas exports actually rose by 1.3%.
The result was a sudden and unexpected shift in the direction of trade. Containers piled up in European and North American ports – having delivered their imports, there was next to nothing for them to bring back to Asia.
This problem was greatly exacerbated in July 2020, when Chinese exports rebounded with unexpected strength. Much of the world’s stock of containers, however, remained stranded in Europe and the US.
While carriers could have theoretically ferried the containers back to Asia, they would have had little to bring with them to make the journey worthwhile.
Waste paper and scrap metal were among the few items of cargo on offer. According to Alphaliner, carriers can currently expect $0.66 per container per nautical mile when travelling from Shanghai to Los Angeles, but only $0.10 for the return trip.
Instead of clearing the backlog, North American ports have continued to accumulate empty containers. According to Hillebrand, only 40 out of every 100 containers that land in North American ports are subsequently sent out again, with the other 60 simply adding to the problem.
A global slowdown in container production due to both Covid-19 restrictions and commodity shortages has added to the crisis. Chinese manufacturers are reportedly now charging $2,500 for a new container, twice as much as in 2020.
Further chaos has resulted from Covid-related port closures, which have led to lengthy delays and queues at the world’s busiest terminals, putting thousands of containers out of action for days or weeks at a time.
The world’s third-largest container port, China’s Ningbo-Zhushan, has been hit by a series of closures due to outbreaks of Covid-19. According to VesselsValue, 71 container ships are currently waiting outside the port.
Globally, 376 container ships are in a similar predicament, representing 2.4 million 20ft containers. The crisis was not helped by the stranding of the Ever Given in the Suez Canal in March, which closed one of the world’s busiest shipping routes for almost a week.
Building more vessels will not materially solve the problem – partly because vessels ordered today mainly get delivered in late 2023 and in 2024. Alan Murphy, Sea-Intelligence
In response to the container crunch, carriers have been racing to increase capacity. Total capacity on the East Asia-North America route, measured in 20ft container equivalents, was 31% higher in July than the same time in 2020, while capacity on the East Asia-Europe route was 20% higher.
Despite these boosts to carrying capacity, just 36% of ships arrived on time in July, according to Sea-Intelligence, down from an average of 74% during 2018 and 2019.
According to analysts, the carrying capacity of ships is not the limiting factor – rather, it is the ability of ports to handle the number of ships and containers necessary to rebalance the global distribution of containers.
“Building more vessels will not materially solve the problem – partly because vessels ordered today mainly get delivered in late 2023 and in 2024, and partly because injecting more vessels will compound the bottleneck problems in ports, effectively increasing the delay time,” says Alan Murphy, CEO of Sea-Intelligence.
“The resolution has to come from solving the congestion problems on the land side. This does not only imply solving the congestion in the ports, but also the hinterland infrastructure related to trucks, chassis, rail, etc.”
Businesses dependent on global shipping are hoping that the Chinese New Year period, during which the country’s exports typically fall as factories close, will offer some respite from the constant flow of containers arriving from Asia.
In contrast to previous years, carriers are not planning a significant reduction in activity over the festive period – likely in the hopes of using the lull to partially clear the container backlog.
With analysts at Bimco expecting freight rates to remain high well into 2022, however, major multinationals are reportedly seeking to regionalise their supply chains.
“A lot of companies are coming to us saying ‘where is the best place to put manufacturing and assembly?’,” Scott Price, president of UPS International, told the Financial Times.
“There is an understanding that reliance on stretched supply chains puts you at risk.”