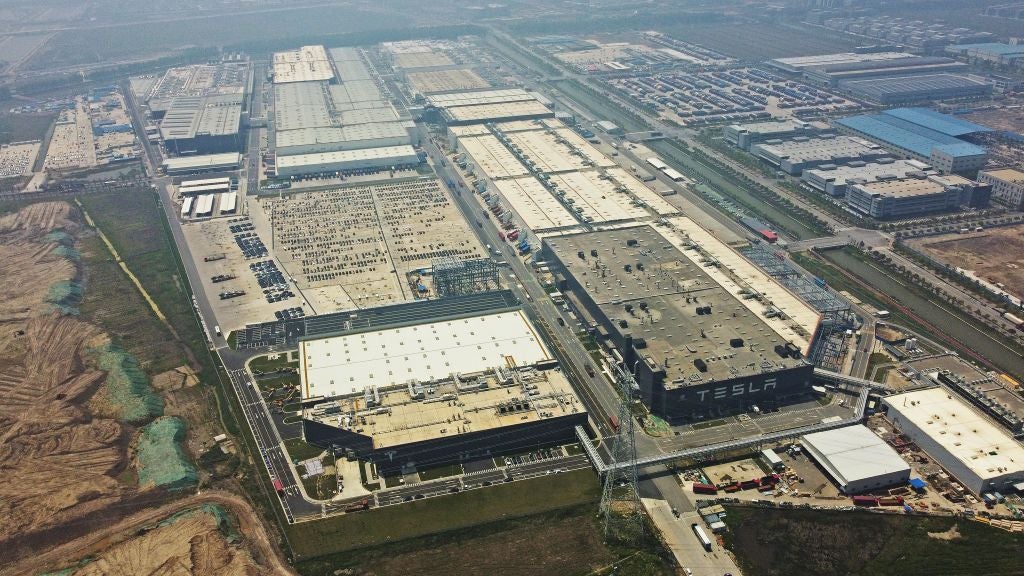
A Site Selectors Guild (SSG) survey released on 17 May indicates that numbers of foreign direct investment (FDI) megaprojects are expected to remain constant or increase over the next five years as the world continues its recovery from the Covid-19 pandemic. The SSG characterises FDI megaprojects as being an investment of more than $1bn in value, creating hundreds, or even thousands, of jobs, typically located on large-scale sites (more than 90,000m2 of land) and with large-scale infrastructure required.
Explaining this growth, Glenn Barklie, chief economist at Investment Monitor, says: “The development of new technologies and trends bring large-scale profit opportunities. Companies are willing to invest large sums in order to harness their market position and be at the forefront of industry developments.”
Indeed, the consistent evolution brought on by industry 4.0 does demand that businesses consistently consider the adoption of advanced technologies in a bid to streamline practices. Alongside this, the supply chain and manufacturing slowdown brought on by Covid-19 has shone a spotlight on the importance of the advantage these advanced technologies can offer.
When asked if, due to their large scale, this means that these FDI projects tend to be in industrial sectors, Gregg Wassmansdorf, chair of the SSG and senior managing director, global strategy and consulting, at commercial real estate advisory and services company Newmark, says: “[Megaprojects] do tend to be more industrial. Technically, they can be services focused. The construction of a 40-storey office building or a corporate headquarters with lots of job creation could qualify as a megaproject, but the majority are industrial or have an industrial-type footprint.”
Wassmansdorf highlights a number of industrial sub-sectors likely to see megaprojects, including automotive, semiconductors, life sciences, aerospace and petrochemicals.
Megaprojects plug into electric vehicle sub-sector
When looking at which sectors are most likely to benefit from megaprojects, 98% of SSG members picked automotive and electric vehicle (EV) batteries. A reason for this could be a combination of the race towards carbon neutrality and the rising demand for EVs.
On this, Barklie says: “With many countries setting climate targets and many companies pledging to become carbon neutral, the realisation of the need to redevelop old, standard processes has come to the forefront of company plans.”
He goes on to explain that while the initial cost of creating new factories, training workers and purchasing new equipment would initially be high, these costs would eventually diminish over time, while “demand for EVs will only ever increase”. This appears to be a legacy pattern for manufacturing projects.
“Original equipment manufacturing projects have always been majorly coveted,” says Wassmansdorf. “They tend to be big in scale, create lots of jobs and function through just-in-time manufacturing, meaning that the supply chains are tight and companies and suppliers will cluster near to them to accommodate those production and delivery schedules. That is what is happening now with EVs.”
As the demand for EVs rises, the creation of these industrial ecosystems will create greater need for megaprojects.
What about the nearshoring trend?
If EVs lend themselves to tightly clustered megaprojects, does this point to the continuation of shortened supply chains? Wassmansdorf thinks so.
“Interestingly, one of the things we asked SSG members was whether or not they believed that megaprojects were more or less internationally competitive,” he says. “Some 43% said they thought these projects were less competitive because essentially it comes back to this rise in regional strategies.”
Wassmansdorf explains that if a semiconductor business, for example, decided to stop sourcing from Asia and was only interested in serving the US market, that Asian semiconductor part is no longer as internationally competitive.
For megaprojects, Wassmansdorf explains that the competition is now much closer to the site location. “It is the US versus Canada versus Mexico,” he says.
On the topic of regions, North America was highlighted in the report, with 100% of SSG members selecting it as most likely to see high growth in megaprojects. Asia was second with 64% of the vote and Europe third with 43%.
When asked to elaborate on why North America came out on top, with the caveat that the majority of SSG members are based in the US, Wassmansdorf highlights the shift away from an Asia focus following the Covid-19 pandemic as a reason for North America scoring highly.
“It is a combination of US companies deciding to keep production at home and businesses in regions such as Europe and Asia looking for a market entry strategy into the biggest consumer market in the world – which would be the US,” he adds.
Labour, labour, labour
When asked what the most important factors were for site selecting megaprojects, the availability of a skilled workforce came top of the list with 69% of the vote. Sufficient space (67%), infrastructure (40%) and competitive incentives (31%) came second, third and fourth, respectively, with operating cost (21%) coming bottom of the list in fifth place.
Wassmansdorf says: “The old mantra in real estate is location, location, location. If you ask site selectors, they will say labour, labour, labour. It is the number one concern in the boardroom.”
How does the ongoing labour shortage in the US and Europe impact the possible successes of these megaprojects? Wassmansdorf explains that there is time to address this and highlights reskilling and upskilling as crucial for companies, and not just in megaprojects. He adds that the quest for a lasting pipeline of talent is always going to be a key endeavour when site selecting.
So which kinds of location are best prepared to take advantage of this thirst for megaprojects? “It depends on the location,” says Barklie. “Locations with large populations that have high levels of education will be fine (and highly competitive). Smaller locations will find it hard to compete.”
There lies a tricky balance to be struck, as often built-up metropolitan areas with well-educated talent pipelines do not have the space needed to facilitate megaprojects. Wassmansdorf explains that the implementation of megaprojects and the creation of the talent pools to attract them is a long-term endeavour that could take countries, states, cities or towns somewhere between three years to a decade to build.
Regardless, the news of this growing appetite for megaprojects is positive for the recovery of FDI flows in a post-pandemic world, but only those locations that can offer the right infrastructure, talent pools and incentive programmes are likely to feel the benefits of this.